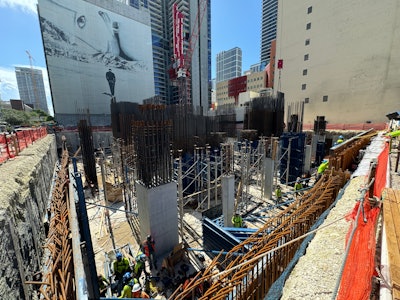
How would you go about staging 1,400 concrete loads in a continuous 36-hour placement? new hotel/condo construction is being undertaken along the waves of the Biscayne Bay and beneath the Miami heat.
A structure of many firsts for many, the 18-ft. deep foundation of the new Waldorf Astoria Hotel and Residences had a special set of challenges. Construction began July 2022 and the mat slab was placed June 2024, with a January 2028 completion.
Seen as almost three different projects in the same structure, the super-tall hotel and condo Waldorf Astoria building is planned to be 10,134 ft. For marketing purposes, it will have 100 stories and 93 construction levels. Offset stacked cubes will shift as the building climbs into the sky. Rendering of the Waldorf-Astoria Miami building.Property Markets Group
The Waldorf Astoria Hotel and Residences – Miami project is managed by Property Markets Group (PMG). Jessica Berthin is the Senior Project Manager. Originally out of New York, developer Property Markets Group moved their headquarters to Miami about 15 years ago. They’ve been developing the skyline of the South Florida, Orlando, and West Coast of Florida since then. They have also done projects in Atlanta, Nashville, and a development in the greater Denver area. They have an in-house construction project management team but subcontract general contractors and concrete work. For South Florida work, their long-term partner in construction has been Boston-based John Moriarty and Associates (JMA).
The concrete contractor on the job was Capform Inc. Capform was founded by Mario Dozo in Carrollton, Texas, back in 1971 and opened operations in Florida in 1987. With experience of working on tall buildings, they were a match for the Waldorf Astoria project. Anderson claims that his team built 5 of 9 tallest buildings in the state.
“If it's concrete, we’ve done it all,” says Capform’s CEO Francisco Anderson. “We’ve done really small projects. We’ve built some high-end/high-profile single-family homes. To date, some of our largest projects include the Dallas Cowboy Stadium.” Due to the demand in the South Florida area, they’re very much geared toward the high-rise market.
Capform designs, engineers, manufactures and owns all their formwork.
Additional concrete subcontractors were concrete supplier Supermix and CNC Concrete Pumping. Rebar installation was by Titon Builders.
“We’ve poured a lot of these large continuous mat pours. Waldorf was not the largest from a volume standpoint, but it’s definitely the deepest mat we’ve ever placed,” notes Anderson. Even at its 18-ft. deep placement, it was the same concerns any contractor would keep an eye on: heat of hydration and keeping the mat cool.
A first super-tall for PMG as well as the hotel brand, Berthin is excited for the design. The tallest Waldorf previously was 35-40 stories in New York City, Central Park off of 5th Avenue.
“Building after Surfside in general, in the state [and] throughout the country has really changed. Here in Miami, the City of Miami has implemented changes in to how buildings are built now,” she adds. “How not to cause lots of vibration for the neighbors, to not affect neighboring structures.”
One of the challenges was the planning of the basement and foundation with water—construction hits the water table at about 3 ft. In order to not have to use traditional sheet piling, they opted to use a deep soil mix where they improve the soils by injecting grout before excavating. Essentially making the soil more rigid. Berthin likens it to improving cake batter so that when contractors dig and install perimeter bracing/shoring walls (that are not sheet pile), there is no water intrusion.
Property Markets Group
“It costs three times the amount of traditional sheet piling, but it’s less noisy,” says Berthin. “It’s much, much, more efficient and you save a lot of money on the dewatering (which is understandably, a big expense in South Florida).” While the project isn’t the first time this method is used in the area, it is for the area’s super-tall buildings.
Another “first” feature for the teams involved and the City of Miami is the eventual installation of a tuned mass damper, which is basically a pendulum weight at the top of the building that counteracts sway to help keep super-tall skyscrapers rigid.
At time of the interview, this construction was also the largest construction loan in the state of Florida.
Being in South Florida, there are other implications. For one, hurricanes. Being built seashore adjacent at a mere block from the coast of Biscayne Bay, the structure will have to contend with wind pressures, wind loads, and everything that comes along with the location. Cantilevers will be strategically placed to be optimal for those wind loads for stability and to keep it as rigid as possible.
Property Markets Group
Logistics & Placement
Doing construction in Downtown Miami has its own challenges. But getting concrete to the location was another special undertaking. The site sits directly across of the Bayside Marketplace and near the Kaseya Center (formerly known as the American Airlines Arena) home to the Miami Heat.
Placement began in the summer but a concert was happening every weekend. It was challenging to find the continuous days. “We knew it would take up to 36 hours of a continuous pour,” says Berthin. “That means you need to make sure that the number of trucks can freely circulate continuously.” About 1,400 trucks were expected to need to travel from the highway, down the main avenue, and along any traffic at the Kaseya Center. All these factors left one weekend to get the concrete onsite where the ramps and roads were going to be open, the weekend of June 14. Further complicating the initial pour was a Justin Timberlake concert putting more traffic along an already busy main road that all 85 trucks would need.
One of the bigger challenges was getting approval on how to get the trucks in and out from local fire and police departments, special event management, the city building department, and public works. More challenges came from ramps closing in the evenings and during the week for a bridge construction. PMG also created a back-up plan in case FDOT needed to close the ramps using a secondary exit.
The plan placed 15 police officers along the route at any given time. PMG rented a staging area across from the arena to act as a staging area to allow concrete to wait should traffic become backed up then head to the site. It was barely used.
Property Markets Group
“Once things started flowing, it really was very seamless and smooth,” says Berthin. “There are so many parties that we have to coordinate with, it was a huge lift.” The general contractor and every subcontractor needed constant communication—not to mention the neighboring businesses: two museums, the port, part of Miami Dade College, another hotel, and two condos.
Placing the foundation at the site was 10 trucks pouring at any given time: 5 concrete pumps with 2 trucks per pump. Turning into the site, connecting to the pump, finishing that truck, and getting it sent over to be washed down before exiting to the street took no more than 10 minutes.
Eventually, they ended up needing 1,200 loads—about 12,440 cubic yards of concrete. Only 6 were rejected for the slump not being adequate.
The biggest challenge on the safety side in working with these very deep mat pours is keeping people secure. “Walking on steel and not level ground…it’s always a changing environment. You build areas where you can safely have workers be able to work without being tied off—and you have to separate those areas from places that are a falling hazard. You have to be able to create anchor points to be able to tie off. That keeps happening through the course of the building.”
Knowing it was June in the south of Florida, the mix was designed with the temperature in mind. “Generally speaking, our structural designer had wanted the concrete mix to stay 185 degrees and not above,” says Berthin. The 8,000 psi mix included 60-70% slag to keep the temperatures down. The main plants sourcing the concrete used sprinklers to keep the aggregate cool prior to mixing. Insulation blankets were used on the mat to keep the temperature regulated during the day.
Capform is used to massive projects and that experience surely was a major factor in the successful placement. “It’s a huge coordination effort,” says Anderson. “I think this was probably one of the smoothest as far as how well the process went. The huge contributing factor to it was the level of coordination with not only your subcontractors, the customer, the general contractor, and local authorities."
Berthin’s advice for contractors: plan. “The whole thing is a lesson learned,” she says. “The scale of the project, that’s the exciting part for me. I’ve done mat pours before, they’re fine, but when you do it on the scale—it becomes a challenge. Because of the scale, you really have to start planning and implementing plans earlier on. The more you could do that, I think that’s the one lesson learned.”
Property Markets Group