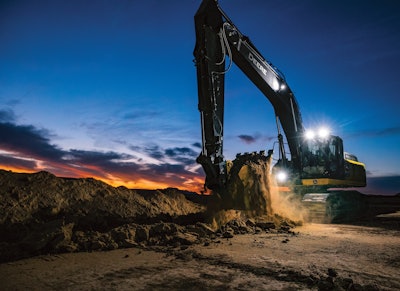
The lack of young talent entering the construction industry and an exodus of veteran operators retiring or moving to a different career have created a shortage of experienced, skilled labor. Quality and productivity must be maintained, shifting the focus toward technology as a way of closing the skills gap.
Contractors who have not updated their machines or fleets with autonomous controls may have struggled to compete because basic, traditional equipment requires dead reckoning and an escort of grade checkers and surveyors to minimize the multiple passes required to get a surface prepped to spec. Lost time, wasted material, inability to adjust to changing conditions on the fly and added rework are forcing old-guard operators to modernize.
Meanwhile, machine and grade control technology only gets more sophisticated, cheaper and easier to install. It’s not unusual for owners of older equipment to install a simple 2D control unit on a machine and suddenly inject new life into an aging investment.
“It’s easier than ever to get into the game,” said Cameron Clark, earthmoving industry director for Trimble. “Tiered solutions exist that can take you from entry-level technology add-ons for basic bucket and blade control up to laser, global positioning system (GPS), onboard diagnostics and full 3D control, all installed on an existing piece of equipment.”
Original equipment manufacturers (OEMs) have been designing different levels of machine and grade control automation into their earthmoving equipment since the late 1990s, when research and development teams began experimenting with smart technology for construction applications. Early solutions evolved from basic hydraulic valve controllers and lasers to onboard hardware sensors and software that automatically read a machine’s position in relation to a surface and adjust to match the design—a science that has gotten more precise with every passing year.
Adding control technology on an existing machine is simple. You simply bring the vehicle into the shop for a day. The sensors get mounted, calibrated. and tied to the electronics. Then the process is is complete.Topcon Positioning Systems
As Oscar Cantu, construction content manager at Topcon Positioning Systems, puts it, “There’s no sacrifice involved in putting control technology on an existing machine. You simply bring the vehicle into the shop for a day; the sensors get mounted, calibrated, and tied to the electronics; and the surgery is complete. [It is] ready to roll and start producing at a higher degree of accuracy immediately.”
A Basic Upgrade Can Make a World of Difference
Machine control is widely viewed as the first step in the automation trajectory, leading from 2D grading and earth moving to 3D trenching, sloping, digging, and other complex project applications. At its core, machine control relies on the GPS and global navigation satellite system to position a tractor extension to cut a stretch of earth to a prescribed height and level according to a triangulated digital map. Often, an external base station is used to read the satellite signals, then relay the reference points to receivers on the machine that automatically control the equipment in relation to the earth, guiding the tractor along the correct path and plane.
Where 2D control tells the operator the position of his equipment relative to the desired plan—high, low, or on a slope—3D control is better for more complex designs, adding depth and angles to the modeling data and grading scheme.
“While OEMs are working hard to bring next-generation machines to the market, it’s difficult to foresee changing needs in the field that may require different functionalities not already designed into the equipment,” said Joe Baldi, director of new business ventures at Moog Inc. “Fortunately, it’s easy enough to equip these machines with controls that manage grade, payload weight, material conditions and other variable factors just by adjusting the onboard software.”
The very nature of 3D grading involves multi-axis control, calling for an added dimension of automation and visibility. However, even a 2D system without a base station or rover can produce some amazing results.John Deere
A basic system will read a 2D site plan and control grade to within one-tenth of a foot. Add-ons can include:
- External base stations for more precise digital mapping
- Rover components that pick up signals and collect data
- Inertial measurement units to finesse position changes
- Other technology to enhance safety, improve accuracy and minimize waste
3D control offers more precision and accuracy, reading terrain variations through a combination of GPS data, sensors and modeling software that account for X, Y, and Z axes. With 3D machine control, operators can excavate, grade and pave to within millimeters of any given site plan.
Fine-Tuning the Grade for Better Results
If 2D control is considered entry-level technology for machine automation, 3D grade control would be a significant step up. Concerned most often with excavating equipment used in trenching and digging operations, applications may include digging ponds, waterways, drainage features or other complex surfaces where control over a blade, bucket or auger is required to satisfy a plan. Even rock drills and rock saws can be precisely controlled using the technology.
"Trenching for utility infrastructure, curbing and certain landscaping projects come to mind. This is where 3D machine control can really pay off."John Deere
“Some projects call for added flexibility in tight spaces, where a tilt bucket, rotator or boom needs to perform some complex excavation,” said Sean Mairet, group product manager for grade management for John Deere. “Trenching for utility infrastructure, curbing and certain landscaping projects come to mind. This is where 3D machine control can really pay off.”
The very nature of 3D grading involves multi-axis control, calling for an added dimension of automation and visibility. For instance, 3D software onboard a backhoe enabled with GPS capabilities will display a site plan in 3D, showing the exact dozer blade position as it carves or moves the required surface material to spec. The result is a more accurate pass on the first attempt.
2D technology can also perform some level of 3D work using GPS-enabled sonic tracers or lasers with the right software but without the same level of precision. Projects may include rough cutting a trench to a specified depth or grading areas in tight spaces using a compact track loader equipped with the technology.
Connecting Operator to Machine & Machine to Design
An automation upgrade is similar to adding an app on a smartphone once the technology is installed on the asset.Moog Construction
Selectable settings on most control systems allow different users to save their configurations, so the same machine can quickly accommodate a new operator. Likewise, different applications set for different seasons of the year can be saved for future reference, allowing contractors to build a custom library of settings, for example, cold-weather paving or heavy payloads.
“You’re … looking at a two-step connection, either way,” said Cantu, whose company designs, manufactures and distributes precision measurement and workflow solutions. “The solution connects the operator to the machine so that in turn, the machine can connect to the surface and design [that] it’s targeted to prep.”
Getting Results Regardless of the Application or Materials Used
Whether equipped with 2D or 3D technology, automated machine and grade control can achieve project results. Clark’s company provides field solutions, from semi-autonomous machine control to virtual reality. With more than 20 years in the business, he’s seen grade control used on simple residential driveways and car parks to large-scale projects, such as airports and golf courses.
“There’s nothing cookie-cutter about it,” says Clark. “You can program a machine to grade a golf course fairway exactly to spec, causing a ball to roll to an exact spot, just as the course architect intended.”
Rail construction; solar pad preparation; oil and gas platforms; mining operations; and more common applications, such as building pads and road construction can all be prepared artfully and accurately using autonomous equipment.
In addition, different materials can be manipulated accurately by adding sensors to detect stiffness, helping determine the exact level of compactness required for a job. Or sensors can be added to read the temperature of asphalt, for instance, ensuring that the grade is paved at the right setting, without having to remove it and start again.
John Deere’s Mairet assures that even a 2D system without a base station or rover can produce some amazing results.
“Cutting a ditch around a house so that water slopes away from the structure is a good example,” he says. “Add a laser app to the system and you can accurately grade areas in wooded areas, working around tree cover, or finesse a surface inside a building before the concrete gets poured.”
Maximizing Your Investment
The benefits are clear. Autonomous machine and grade control can eliminate the need for bulky survey staking and other manual grade-checking tasks, saving time and money, while also reducing errors and rework. Without a traditional ground crew escorting the machine, not only is labor reduced, but safety is improved.
Last-minute adjustments can be made on the fly using onboard software, without re-staking the job, easily accommodating unplanned changes. The fact that rookie operators can perform all this work with minimal training is an advantage, especially in a tight labor market. Most important, the design plan is met precisely, often on the first pass, creating customer satisfaction and boosting contractor reputation in the process.
Start With Expert Advice
The way to autonomous machine and grade control is straightforward. Expert advice suggests that you ask around, see what your peers have experienced and get a few recommendations before you jump in. Remember, everyone has their preferences, skill level, working style and familiarity with the equipment.
Most technology can be used in diverse ways, so learn what the options are and plan accordingly. Avoid buying more technology than you need.
It’s a good idea to make a list of questions to ask in advance. Dealers and machine and grade control technology companies know their capabilities and are adept at explaining them. Once you feel comfortable with a purchase, request a demo, and try the equipment for yourself before you buy.
Lastly, make sure that your chosen supplier offers adequate support and training on the technology. Schedule a day for your operators to learn the system. Designate a super user, if possible, to serve as your internal trainer. And be sure that your technology vendor can answer technical questions by phone or in the field.
A good, dedicated, tech support team is critical to ensuring that you get the most out of your investment. If something isn’t working right, a quick call to the support desk can be all it takes to remedy the situation.
The Time Is Right to Get More Out of Your Equipment
There’s no reason to delay adopting machine and grade control technology for your business. The technology has been around for decades and has been developed into a fine art. Even novice operators can achieve amazing results.
Using machine and grade control technology can immediately open the door to improved safety, savings, profitability, productivity and a marked competitive edge. Make precision and finesse your best practice. Connect and control your machinery, and experience the benefits of autonomous technology today. Talk to a dealer about the best way to start.