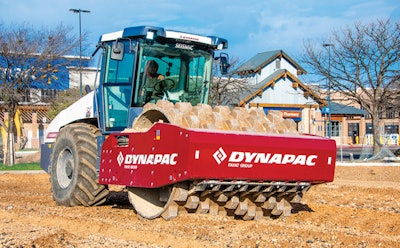
During the past decade, RDC Paving has grown into one of the premier asphalt and concrete paving companies in the Austin, Texas, area. The firm handles a wide range of projects, from sealcoating and striping to constructing large commercial parking lots.
RDC Paving recently took on its first full-depth reclamation project that involved pulverizing and reclaiming the asphalt of a parking lot of a retail store in Buda, Texas. After curb removal, a crew began the reclamation process, which included rebuilding the subgrade.
“We’re going down 10 inches and grading that off,” explained Estimator/Project Manager Greg Fister. “As we rebuild the subgrade, we’re adding powdered Portland concrete and water and compacting it before doing a final grade and laying asphalt.”
Confidence going forward
To ensure maximum compaction efficiency, RDC Paving is using a Dynapac CA6500PD single-drum vibratory roller with an 84-inch compaction width. RDC Paving purchased the machine from local dealer Closner Equipment Co. Inc. with the help of Capital Area Manager Logan Maywald. RDC Paving is a longtime Dynapac user of smaller rollers for its asphalt operations. The CA6500PD was a step outside of the box.
“Because this is our first project of this type, a lot of thought went into making sure we had the budget set right,” said Fister. “Dynapac has always given us excellent results, and Logan has been fantastic for us. We trust him. He said this was the machine we would need, so we decided to go with it. He came out the first day and showed us exactly what we needed to do and helped us operate the machine. The results have been top-notch.”
The 22.7-ton machine features Dynapac Seismic technology that automatically detects the natural frequency of the soil characteristics and works with it to apply the correct amount of energy and achieve better compaction results. That maximizes the contact force between the drum and the ground, yielding maximized compaction and energy efficiency with fewer passes.
“A sensor on the drum detects what kind of soil conditions it’s in,” said Dynapac’s Jerry Hackett, Dealer Sales Manager, South Central U.S. “It sends a signal to the variable displacement pump. This happens in milliseconds, and it adjusts the frequency. Testing showed that we’re getting better and faster compaction versus pounding, which can lead to over-compaction. You can set the target compaction and the machine knows where it is in relation to it. Once the operator sees they have hit the compact material value, they can get the material tested and go on to the next section or project.”
Estimator/Project Manager Matt Teichelmann added, “It quickly helps us push the job forward. We’re able to move a lot faster and meet those compaction densities in a timelier manner, which brings up our efficiency.”
In addition to faster compaction results, the benefits of Seismic include reduced vibration power and energy consumption of up to 30%; decreased noise levels; the possibility of omitting final static passes; fewer compaction passes overall, depending on application; and lower wear for increased machine life. Seismic works with all types of soil.
“Less passes, less fuel, greater savings,” stated Maywald. “Another major advantage with the roller achieving target compaction sooner is that because the operator achieves compaction faster, they can go operate another machine or go perform other tasks and maximize productivity. In a time where operators can be hard to find, that’s a great benefit.”
The CA6500PD also meets the Texas Department of Transportation’s (TxDOT) specifications for foamed asphalt projects, according to Maywald.
“TxDOT requires a certain tonnage for the roller, and this is actually heavier than needed, so it gets the job done quicker,” said Maywald. “It’s great for those types of jobs as well as full-depth reclamation.”
Fister said the CA6500PD has proven to be a perfect fit.
“We have used it every day, weather pending,” declared Fister. “We have had testing done on a daily basis, and we’ve made compaction every time. With the success we see on this project, we have confidence in doing more of these types of jobs going forward.”