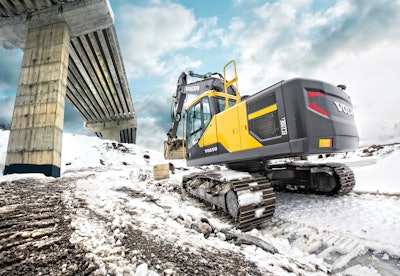
Winter is on the horizon and with it comes environmental challenges affecting equipment and its operators. It will soon be time for winter equipment prep for cold-start conditions and warm-up procedures to ensure that machines operate at peak performance, according to Ted Polzer, director, product and customer support, CASE Construction Equipment.
Preparing Construction Equipment for Winter
For winter work success, many factors must be managed to make sure jobsite operations proceed without interruption.
“Considerations need to be given to your fuel sources and the rating (winter/summer blend) in addition to things like worn tires that inhibit maximum traction and efficiency,” Polzer said.
Cold temperatures can pose problems for liquids such as fuel, antifreeze, batteries, oil and other lubricants.CASE Construction Equipment
“Repeated exposure to snow, ice, and salt brine or sand mixtures can also cause rust, and freezing temperatures can cause the rubber in hydraulic hoses to become brittle,” Danny Freeman, product manager, Volvo Construction Equipment, said. “Slipperiness and low visibility can also create safety issues.”
“Colder temperatures are harder on heavy machinery for several reasons,” said Allen Charnstrom, RDO Equipment Company’s product specialist manager, adding that preparing construction equipment for winter requires more care and attention. “The cooler temperature plus moisture increases wear on the machine’s engine, transmission and hydraulic systems.”
Component Check
Charnstrom explained that engines can “start hard” during low temperatures, affecting different machine components including:
- The increased viscosity of engine and hydraulic oils reduces the ability of engine parts to move and requires more energy to travel throughout the machine.
- Because of diesel fuel’s paraffin, it gels and does not flow as freely.
- Cylinders reduce compression due to cold air’s increased density. The batteries use more of their capacity to “crank” the engine at the required speed for the compression needed for fuel ignition.
Every operator needs to check their machine’s components and then the generator’s fuel level in case they need to operate it through the night.RDO Equipment
According to Charnstrom, operators need to set aside more time to check machine components and engines before winter operations.
“Use any bulk fuel, then drain tank sumps before treating a new batch for colder weather,” he said. “Add in fuel conditioner, and check coolant and freeze protection before replacing the fuel’s filters.”
Charnstrom noted that suppliers can treat fuel for end users in winter.
“About four to six weeks before temperatures are forecasted to change, check and service batteries,” he said. “Consider changing engine or hydraulic oils to a lighter weight to reduce potential wear and promote easier starting. Change grease to a lighter weight in auto-lube systems … as well to prevent injector plugging and dry joints.”
Extra Care Required
Charnstrom shared this checklist to for winter equipment prep operations:
- Engine: Prioritize fuel quality, lubrication and air filtration
- Cooling systems: Verify coolant levels, concentration levels and inspect the cap
- Batteries: Check electrolyte levels, load check and alternator output
- Undercarriage: Conduct daily inspections to remove debris
- Filters: Replace air, oil, and fuel filters
“Operators should have support equipment like generators at remote jobsites to power engine block heaters,” he said. “Consider equipping machines with diesel-fired coolant, fuel and oil heaters for use without electricity.”
Charnstrom also pointed out that operators need to pay attention to site safety, taking extra precautions to clear haul roads of snow and add sand if necessary.
“Sometimes, operators need to use motor graders, dozers or excavators to ‘rip frost,’ which means breaking up the ground to reduce thawing time,” he said. “Ripping frost is hard on any machine, so additional maintenance may be required after the job is complete.”
Equipment checks need to be completed in the morning and evening for proper winter maintenance. Every operator needs to check their machine’s components and then the generator’s fuel level in case they need to operate it through the night.
“Before cooler temperatures, any operator should discuss their concerns with a trusted technician during annual inspections,” Charnstrom said.
Preventive maintenance can improve operations and increase uptime. According to Polzer, prewinter prep provides a great opportunity for this.
“Prewinter is a great time for preventive maintenance on items like air and fuel filters, checking the condition of your antifreeze, performing scheduled oil changes (maybe even considering a viscosity change), and assessing if maintenance is needed on the attachments you plan to run in the cold,” Polzer said.
Contractors working in conditions below 0°F should consider switching to cold-weather hydraulic and engine oils, Freeman noted.
Equipment checks are even more critical during the winter months.Volvo Construction Equipment
Extreme cold can freeze brakes and prevent them from releasing, Freeman said. He added that contractors should preemptively replace fluids with an arctic grade or lower-temp version. He also noted that Number 1 diesel performs better than Number 2 in cold temperatures because its lower viscosity makes it less prone to gel.
“You may also want to consider winter diesel or arctic diesel, which … feature even lower freezing points and better cold filter plugging points,” Freeman said. “Consider additives if the proper diesel blend is unavailable, but don’t use additives you aren’t familiar with. Some aren’t compatible with exhaust aftertreatment components and may render them inoperable.
“It’s also wise to keep your fuel tank at least 70% full to prevent moisture from condensing. I don’t recommend starting fluids. These can damage engine components if too much is added.”
Freeman noted that contractors working where temperatures get as low as -40°F may have to keep machines idling all night to keep them warm enough to run.
“If you must do this, make sure to increase your idle to at least 1,100 rpm, so the engine will create some heat and generate a more efficient burn of the fuel,” he said. “Unburned fuel in the cylinder can lead to washing of the cylinder walls. Just know that long idling burns fuel, adds hours to your machine, elevates soot load and more. Auto-start systems, block heaters and air heaters can be good alternatives.”
As temperatures drop, the recommended concentration of coolant rises, Freeman pointed out.
“Down to -13°F, you can use 40% coolant, but by -31°F, you should increase it to 50% coolant,” he said. “Diesel exhaust fluid (DEF) fault codes from telematics programs should be addressed immediately. Machines are usually designed to run with frozen DEF for a set amount of time before taking a new reading to see if it’s thawed.
“If it’s still frozen and cannot dose, it will send a fault code and/or derate the engine. Check with your dealer or [manufacturer] to see what that determined amount of time is and if the DEF hasn’t thawed yet, shut the machine off.”
Restarting the machine will reset the clock on when the engine control unit will check the DEF temperature again, according to Freeman. That will help get a contractor out of a predicament until the root cause can be found and repaired.
“DEF has a good shelf life if operators follow a proper storage system during winter,” Charnstrom said. “DEF must be stored in new ISO-approved containers in a climate control area of no lower than 50°F.”
“If your machine doesn’t have an auto greaser, you must grease the lines,” Freeman added. “You probably won’t get regular grease to push through the line at low temperatures, so it’s important to prime your system with low-temp grease.”
Oil viscosities at different ambient temperaturesVolvo Construction Equipment
A fully charged battery will be 12.6 volts when checking with a voltmeter. Fully retract the hydraulic cylinder rods when possible and consider steam-washing the machine’s exterior regularly to help remove salt buildup, said Freeman.
“Check hoses frequently for signs of freezing and keep snow and ice off your machines to prevent damage and maintain visibility,” he added.
Gary Roberts, off-highway product application specialist, Shell Lubricants, said that using full-synthetic or synthetic-blend, heavy-duty diesel engine oils can provide advanced engine protection and performance during cold weather.
“These advanced lubricants perform well in heavy-duty diesel engines, especially in extreme hot and cold temperatures, and provide protection that can help save money,” Roberts added. “Low-viscosity engine oils flow more easily in cold weather and make cold weather startups easier, putting less stress on the starter and battery.”
These lubricants also prevent metal-to-metal contact caused by low speeds, high loads, cold starts, shock loading and extended idling—all of which can cause premature engine wear, Roberts noted.
Synthetic lubricants can also help increase fuel economy and operational savings while reducing the carbon dioxide footprint, he added.
“Daily demands on your equipment require engine oil with critical properties … [including] advanced or enhanced viscosity control in extreme conditions to prevent abrasive wear,” said Roberts. “For on-highway vehicles, full-synthetic and synthetic-blend engine oils can help provide enhanced fuel economy capability without compromising engine protection or durability.”
Roberts noted that the most common low-viscosity diesel engine oils are 10W-30 and 5W-40, which are suitable for many modern diesel engines and can provide the same level of protection as 15W-40 with some important benefits.
“The 10W-30 and 5W-40 oils flow through the engine quicker on cold start-ups, causing less friction to be generated in the engine, which will prevent engine wear,” said Roberts.
Regarding coolants in winterization preparations, Shell Lubricant Solutions typically recommends using a 50/50 mixture of ethylene glycol and water in heavy-duty diesel engines.
“The ethylene glycol helps prevent freezing and raises the boiling point,” Roberts said. “Water is necessary because it is more effective at heat transfer than ethylene glycol. The 50/50 mixture gives a combination of good heat transfer and effective freeze protection down to roughly -34°F. A slightly higher concentration of ethylene glycol may be considered in extremely cold environments.”
A growing segment of vehicles and equipment now require nitrite-free, engine antifreeze/coolant formulations to better protect aluminum components, Roberts noted.
“Nitrite-free coolants provide improved protection of aluminum components, including modern brazed aluminum heat exchangers, and meet many of the latest [manufacturer] specifications,” he added.
Onsite conditions are often unpredictable, and this can impact pins, bushings and bearings, said Roberts. Having a plan to safeguard these components is imperative.
“To protect components and keep them moving as they should, a high-quality grease that can maintain performance—even in the harshest environment—is required,” he added. “It is important to consider a range of greases that can deliver a reliable level of performance, provide mechanical stability to avoid breakdowns, oxidation stability for system efficiency, and water washout resistance for excellent corrosion protection.”
Always be certain to use greases that meet equipment specifications, Roberts noted.
“Typically, many end-use grease customers will utilize a National Lubricating Grease Institute (NLGI) #1 grade grease instead of a NLGI #2 grade in colder temperatures [because of the] better pumpability due to its lower thickener percentage,” he said.
The accumulation of moisture in hydraulic fluid can cause corrosion and premature mechanical wear. Moisture accumulation is typical in cold weather as the temperature fluctuates.
“This can alter viscosity, deplete additives and instigate sludge formation in hydraulic oils,” noted Roberts. “Hydraulics utilize air to ‘breathe’ as they operate, which is a primary source of how moisture and contamination can enter lubricant reservoirs. Using high-quality desiccant breathers can reduce particulate and moisture contamination in hydraulic fluids on mobile construction and stationary equipment.”
Operator Concerns
Operators need to set aside more time to check machine components and engines before winter operations.RDO Equipment
“Depending on how bad the conditions are, lights and wiper blades icing up can affect visibility,” Polzer noted. “A good practice is to use the best washer fluid to help mitigate the buildup. Spare wiper blades are always good to have on hand, but covering the glass or the wiper blades when not in use can help prevent frustrating ice buildup ... This speeds up time getting the machine to work versus clearing windows and waiting for them to thaw.”
Thorough daily machine inspections and following proper operating procedures prevents accidental wear and tear or downtime, according to Freeman. This includes:
- Let machines warm up and cool down to let the engine stabilize
- Start moving the machine slowly to warm up the whole system and hydraulics
- Give the equipment a couple minutes of idle time at the end of the day before completely shutting down
Engine block heaters can help warm the engine before starting, said Freeman.
“Diesel-powered coolant heaters also help with cold-weather startup and warming the cab and water separators with heaters helps minimize wax buildup in [the] fuel,” he added.
According to Freeman, contractors may need to work the machine harder to allow it to perform passive regeneration.
“Sometimes normal operations just aren’t enough to heat the exhaust so [that] it’ll perform a regen, and excessive idle times can prevent proper heat-up,” he added. “If the machine never gets warm enough to perform passive regeneration, you can end up in a fault situation.
“Consider a regen at the end of the day if the soot level is high instead of waiting for the next day when the engine is cold. This will help ensure [that] you can start the engine with a clean exhaust on a chilly morning.”
If a filter includes a drainage bowl, operators should drain it nightly to prevent the water from freezing and cracking the bowl.Volvo Construction Equipment
In addition, operators should “check the alternator belt for wear and damage and [examine] glow plugs or air intake heaters if you have them,” he said. “Arctic-rated hoses can handle conditions down to -40°F. Service your fire suppression battery monthly. The extinguishing agent function range is -22°F to 140°F. Be sure [that] all lights are in working order and you can clearly see everything around you. Keep stairs and walk areas clear of snow and ice to help prevent accidents.”
Test products or steps being added to a process ahead of the cold season to ensure their readiness, Freeman advised.
“Swapping in fresh filters before temps drop will also help make sure the engine isn’t starving for fuel and oxygen [caused by] plugged filters,” he added.
Undercarriage Changes
Operators should clean machines—tracks, undercarriage, driveline, articulation joints and steer cylinder—daily.Volvo Construction Equipment
“Air pressure is also especially important to maintain and consider in tires equipped with chains to maximize traction and impact,” he added.
Freeman advises to clean machines—tracks, undercarriage, driveline, articulation joints and steer cylinder—daily.
“If they get muddy and it’s below freezing, they’ll freeze overnight,” he said. “Frozen mud is a lot like concrete. It’s much more difficult to chisel and pry out than ice and can cause serious damage to tracks, pins and rollers if an operator tries to run the machine with it still there.”
“Depending on the specific temperature, moisture level and soil type, a machine’s tracks may need to be loosened based on the amount of material that gets packed into [the] tracks,” Charnstrom said. “Early in the fall or winter season, operators should discuss situations with their fleet managers, so they can understand when they can add tire chains if necessary.”
Electric Equipment Concerns
It is said by some that electric equipment does not operate well in cold temperatures. Freeman said that this is a myth. Electric equipment can work in colder temperatures.
Diesel engines are harder to start and take longer to heat up to operating temperature than battery-electric equipment.Volvo Construction Equipment
To improve battery performance during winter, Freeman advises contractors to store machines inside overnight so that the batteries reach indoor temperatures.
“If you can, charge your machine indoors, too,” he added. “Volvo electric machines have an optional programmable cab heater allowing you to choose the days and times you want to get into a prewarmed and defrosted cab.”
Electric machines require less maintenance than diesel models, including in cold temperatures, Freeman said.
“Diesel engines are harder to start and take longer to heat up to operating temperature,” he added. “With electric machines, there’s nothing to be serviced around the electric parts … other than doing a visual inspection as needed.”
Start Winterizing Before Winter
Contractors should start winterizing equipment prep at least six weeks before the forecasted temperature dips.RDO Equipment
“Contractors should stock up [on] batteries, treated fuel and filters during the fall,” he said. “Contractors working in different regions should plan extra service time when they move one machine from a warmer southern state to colder northern states to prevent coolant, fuel or oil issues.”
Many equipment dealers will have promotions for annual inspections during the fall. Contractors can talk to trusted partners to stock up on materials and schedule preventive winter maintenance, Charnstrom said.