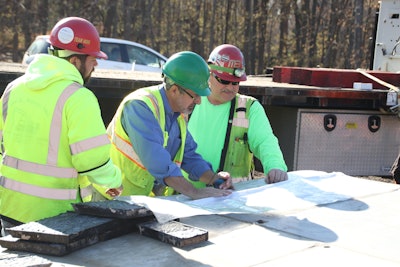
As the concrete industry evolves under the dual pressures of climate responsibility and resource scarcity, a new paradigm has emerged — one that prioritizes sustainability not as an afterthought but as a fundamental framework. The circular economy, long championed in manufacturing and materials science, is now taking root in the concrete construction sector. And while much of the attention has centered on cement production and material sourcing, concrete contractors themselves play a vital, if often underappreciated, role in implementing circular economy strategies on the jobsite.
Concrete contractors have traditionally operated at the point of application — placing, finishing, and curing the material according to specifications. But in an era when lifecycle performance and environmental accountability are redefining project value, concrete contractors are now critical decision-makers in the design and execution of sustainable construction strategies.
Perhaps the most direct way contractors contribute to circular economy goals is through the repair, rehabilitation and protection of existing concrete structures.
While contractors may not formulate cement or manufacture admixtures, they do influence the material selection process — particularly during pre-construction collaboration and submittal stages. By working closely with producers and specifying engineers, concrete contractors can advocate for circular mix designs that incorporate recycled content, reduce embodied carbon and enhance durability through performance-based criteria rather than prescriptive norms.
This shift requires technical fluency in both material science and lifecycle engineering. Contractors must understand the behavior of supplementary cementitious materials (SCMs) like fly ash, slag and silica fume, as well as the performance parameters of recycled concrete aggregate (RCA). With this knowledge, they can support mix optimization strategies that reduce environmental impact while maintaining or even improving workability, setting time, pumpability, and finish quality.
Extending the Useful Life of Concrete Structures
Perhaps the most direct way contractors contribute to circular economy goals is through the repair, rehabilitation and protection of existing concrete structures. Instead of defaulting to demolition and rebuild — a process that generates massive waste and demands energy- and carbon-intensive virgin materials — contractors can deliver long-term value by extending the service life of aging assets.
Modern repair systems go far beyond cosmetic patching. High-performance mortars, fiber-reinforced overlays, and carbon fiber strengthening systems allow contractors to restore structural capacity, address chloride-induced corrosion, and mitigate freeze-thaw damage with surgical precision. These interventions often involve advanced diagnostics, such as ground-penetrating radar or half-cell potential mapping, to target repairs accurately and minimize material use.
Protection technologies like breathable sealers, silane-based water repellents, and chemically resistant coatings further extend durability by defending against moisture ingress, sulfate attack, and alkali-silica reaction. When integrated into maintenance programs, these products help infrastructure resist the harshest environmental and load conditions — transforming reactive repair into proactive preservation.
Field testing on the jobsite helps drive innovation in concrete performance and quality control.Euclid Chemical
Resource Recovery & Jobsite Integration of Recycled Materials
Contractors who understand the hydration kinetics and compatibility of SCMs with various admixtures are better positioned to optimize mixes for specific jobsite conditions.
Circularity in concrete construction also depends on turning what was once waste into viable input. Contractors increasingly encounter opportunities to use recycled materials not only in their concrete mixes but also across site development applications. Crushed concrete from demolition, for instance, can be repurposed as base material for roadways, building pads, or even reintroduced as aggregate in structural mixes when appropriately processed.
This closed-loop approach to materials management relies on a contractor’s ability to coordinate with recyclers, understand grading requirements, and ensure performance specification compliance. With modern quality control processes and third-party certifications, RCA is a technically viable and often cost-effective option — especially in urban markets with limited access to virgin aggregate sources.
Similarly, contractors who specify SCMs in their mix submittals help divert industrial byproducts from landfills. These materials not only reduce the demand for Portland cement — responsible for roughly 8 percent of global CO₂ emissions — but also improve the rheology and chemical durability of the finished concrete. Contractors who understand the hydration kinetics and compatibility of SCMs with various admixtures are better positioned to optimize mixes for specific jobsite conditions.
Beyond traditional recycled materials, emerging technologies equip concrete contractors with new tools to contribute to carbon reduction. Carbon mineralization techniques, for example, inject captured CO₂ into fresh concrete, where it reacts with calcium ions to form stable calcium carbonate — permanently sequestering emissions and enhancing compressive strength. Some ready-mix producers now offer these mixes commercially, and contractors who understand their curing behavior and performance profile can confidently incorporate them into structural work.
Carbon capture, utilization, and storage systems at the plant level are also transforming the material supply chain. While contractors may not operate these facilities, they are increasingly responsible for verifying the embodied carbon footprint of the materials they place. Environmental Product Declarations, now common on public and LEED-certified projects, offer transparency and a benchmarking tool. Contractors who can interpret and communicate these metrics will be at a competitive advantage as carbon disclosure becomes the industry norm.
Financial Realities: Making the Circular Business Case
In a competitive market where sustainability is increasingly seen as a proxy for innovation and risk mitigation, contractors well-versed in circular strategies are positioned as value-added partners rather than commodity service providers.
Despite the environmental urgency, circular practices must deliver economic value to achieve mainstream adoption. For concrete contractors, that value often manifests in reduced lifecycle costs, increased bid competitiveness, and eligibility for high-value public and private projects.
Repairing rather than replacing a structure, for example, avoids not only material and labor costs but also expenses tied to demolition, hauling, and downtime. Using recycled aggregate or SCMs can mitigate price volatility in virgin raw materials and may qualify a project for green building incentives, tax credits, or preferential procurement programs. In a competitive market where sustainability is increasingly seen as a proxy for innovation and risk mitigation, contractors well-versed in circular strategies are positioned as value-added partners rather than commodity service providers.
Collaboration Across the Value Chain
Circularity demands coordination at every stage of the project lifecycle. Contractors must collaborate with material suppliers to vet low-carbon options, work with design teams to ensure constructability of innovative systems, and educate owners on the long-term value of preservation and lifecycle thinking.
This collaborative mindset extends to regulatory and industry bodies as well. As building codes evolve to incorporate embodied carbon thresholds and performance-based specifications, contractors who actively participate in pilot programs, technical committees, and continuing education will help shape the standards that govern tomorrow’s concrete construction practices.
Ultimately, the transition to a circular economy is about more than sustainability — it is about resilience. Concrete will remain a foundational material in our built environment. The question is whether we can deploy it in ways that conserve resources, adapt to changing demands, and extend the usable life of critical infrastructure.
Concrete contractors are uniquely positioned to lead this transformation. By championing circular principles — through smarter material selection, advanced repair and protection, and resource recovery on the jobsite — they can deliver structures that are not just built to last, but built to evolve.