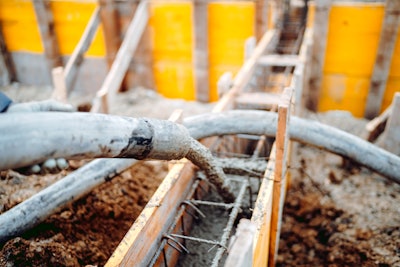
Marianna Kopsida, PhD, industry manager - IMF & Vertical Construction at Trimble, shares her insight into the state of the concrete industry and the challenges contractors are managing daily. Concrete Contractor connected with Kopsida over email in June 2025.
Q. What have been the biggest challenges for concrete contractors so far in 2025?
Marianna KopsidaTrimble
Q. What has been happening to address these challenges?
Contractors are also adopting machine control for accurate placement of materials.
Contractors have responded by accelerating the adoption of technology and optimizing project planning. To address these critical challenges in field productivity, there's a strong industry push towards integrated digital workflows and connected construction platforms. Solutions like Trimble Connect are actively bridging the gap between design, pre-construction, and field execution, aiming to provide a "single source of truth” and to connect the right information to the right people at the right time. This involves leveraging BIM (Building Information Modeling) for detailed concrete designs, connecting those models directly to the field. These efforts have been moderately to highly impactful for early adopters; they've demonstrably reduced layout errors by providing accurate digital models directly to the field, streamlined communication by centralizing RFIs and design changes, and improved overall throughput by optimizing equipment utilization. However, widespread adoption still requires significant investment in technology and cultural shifts within contracting firms.
Contractors are also adopting machine control for accurate placement of materials. This can range from 3D printing machines with automated heads for pouring and also concrete pavers. Adoption has increased since the beginning of the year to manage yields and keep concrete costs down. There is also the added benefit of not needing to place stringline to guide the machines, meaning surveyors aren’t showing up prior to paving. The job can start when the paving crew is ready and surveyors can concentrate on higher value workflows.
The adoption of modern and unified estimating, operations and financial management software is also helping to address these challenges. Faster, more accurate bidding; including easier access to previous actuals - win the right jobs at the right margins. Real-time, online resource scheduling and dispatching provides company-wide visibility resulting in efficiency gains and being able to dynamically adjust having the right people, equipment, and materials to the right place at the right time.
The skilled labor shortage remains a big challenge in 2025, across all specializations and especially for finishing crews and formwork specialists
Q. Where are concrete contractors at with employment and the skilled labor shortage?
The skilled labor shortage remains a big challenge in 2025, across all specializations and especially for finishing crews and formwork specialists, which directly impacts field productivity. Some contractors are making headway by tapping into nontraditional labor pools, partnering with trade schools, and using technology and automation to reduce dependency on skilled labor. Some contractors have adopted robotic layout and reality capture tools to bridge the labor gap and boost jobsite efficiency.
Q. What segments of concrete construction have seen growth in 2025?
Commercial and precast concrete segments have seen notable growth in 2025, largely driven by data center and warehousing construction. The tilt-up market is also rebounding due to its efficiency for large, repeatable structures, such as hotels and hospitals. Conversely, residential concrete—especially single-family developments—has narrowed due to interest rate volatility and softening housing demand. Public infrastructure (road and highway) remains steady but is facing budget constraints, limiting large-scale starts. Factors such as AI-driven logistics, sustainability mandates, and prefabrication trends are fueling the segments that are growing.
I anticipate that the growth in industrial and logistics concrete construction will remain strong.
Q. How do you think this growth/narrowing will track going into 2026?
Going into 2026, growth in commercial and industrial concrete is likely to continue, especially with federal investment in domestic manufacturing and digital infrastructure. I anticipate that the growth in industrial and logistics concrete construction will remain strong, as companies continue to optimize supply chains and expand automated facilities, demanding highly productive concrete flooring solutions. Similarly, public sector investment will likely sustain the positive momentum in Infrastructure projects, particularly those involving large-scale concrete paving and bridge decks. Precast and tilt-up will continue gaining traction as contractors seek to minimize site labor and accelerate project schedules.
Q. How are contractors handling economic challenges?
Concrete contractors are handling economic challenges primarily by prioritizing field productivity and leveraging technology to maximize output with existing resources. They are investing in digital tools for more precise estimating and project management, which helps to optimize material usage and labor allocation, thereby protecting slim profit margins directly on the jobsite. There's also a clear trend towards strategic equipment investments in areas that offer immediate productivity gains, such as robotic layout tools and laser scanners.
The same investment in technology is being seen in the machine control space. Several contractors have made their first technology purchase in 2025 on their concrete paving machines to maximize efficiency and get the most out of their current fleet of equipment.
Uncertainty in material costs directly impacts bidding accuracy and forces contractors to invest more time in price validation and alternative sourcing, indirectly reducing overall project management efficiency.
Q. How have they been impacted by tariffs?
Tariffs, particularly on imported steel products used in rebar and structural components, have had a direct and impactful effect on the operational costs and planning for concrete contractors. For instance, the ongoing tariffs have contributed to volatile and often higher prices for rebar, a critical component in nearly all reinforced concrete structures. This means a contractor might have to factor in significant cost increases for a major slab or foundation project, sometimes experiencing price surges mid-project that eat into profit margins or necessitate difficult negotiations with clients. For instance, a contractor on the West Coast faced an unexpected 14 percent increase in formwork system components due to new tariffs on Chinese steel, which forced them to delay a project start by several weeks while sourcing alternative suppliers. These types of disruptions have made procurement planning far more complex and less predictable. This uncertainty in material costs directly impacts bidding accuracy and forces contractors to invest more time in price validation and alternative sourcing, indirectly reducing overall project management efficiency.
Modern construction software solutions can centralize financial, operational and project data, helping companies identify cost increases linked to tariffs and adjust procurement strategies accordingly. These solutions also enhance project planning and forecasting, with real-time cost tracking and financial insights to help control expenses and plan for long-term stability.
This improved economic climate should alleviate some of the pressure on material costs and project financing, creating a more favorable environment for concrete contractors to invest in productivity-enhancing technologies and expand their operations.
Q. What do you expect the economy to do for the remainder of 2025 and 2026?
For the remainder of 2025 and into 2026, I forecast a period of cautious but steady economic growth, with a gradual easing of inflationary pressures and a more stable interest rate environment emerging, which should indirectly benefit concrete contractors by stimulating project starts. We anticipate a slow and steady recovery in global construction output, with modest gains in 2025 translating into more robust growth in 2026, particularly in sectors driven by public investment. This improved economic climate should alleviate some of the pressure on material costs and project financing, creating a more favorable environment for concrete contractors to invest in productivity-enhancing technologies and expand their operations.
Q. What technological areas do you see the potential for innovation?
I see immense potential for innovation in the application of Artificial Intelligence (AI) for real-time field optimization and quality control in concrete pours. These solutions could process live data from sensors embedded in concrete and site conditions to provide immediate, actionable insights to field crews, guiding optimal curing practices or identifying potential issues. Furthermore, advanced robotics and autonomous equipment for concrete placement and finishing are poised for significant breakthroughs. These innovations aim to directly address the critical issues of labor scarcity by automating repetitive and physically demanding tasks, significantly enhancing on-site precision, and boosting overall field productivity.
Artificial intelligence will have the biggest potential to change things for concrete contractors for the better by revolutionizing field productivity through predictive insights and automated quality assurance. AI has the capability to analyze vast datasets of project variables to offer more precise, real-time guidance to crews. Furthermore, AI-powered tools could provide insights for flatness, levelness, and surface defects, instantly flagging deviations from design specifications. This proactive identification of issues directly reduces costly reworks, ensures higher quality finishes, and significantly boosts overall on-site efficiency by making field operations smarter and more data-driven.
Q. What innovations would you like to see developed in concrete equipment and tools?
I would like to see more usage of BIM models and cloud-based connected workflows in the industry, and wider adoption of such connected workflows. Rather than entirely new tools, what’s most needed in 2025 is broader and more seamless adoption of technologies that already exist — particularly those that bridge the gap between digital design and field execution. Robotic total stations, 3D scanners, and BIM-integrated layout tools have matured significantly, but adoption across the concrete sector remains uneven. Contractors would benefit from simplified workflows that connect BIM models directly to these tools without requiring specialized operators or extensive retraining. For example, making it easier for foremen and layout crews to extract real-time data from models, push updates to field devices, and verify as-built conditions using accessible platforms could drastically reduce rework and boost jobsite efficiency.
Q. What do you expect the biggest challenge(s) will be in 2026 for the concrete industry?
In 2026, I anticipate the biggest challenge for the concrete industry will be the simultaneous pressure to rapidly adopt advanced digital and automated technologies to boost field productivity, while also navigating the complexities of sustainable materials and volatility of costs into daily operations, all within the context of a persistent skilled labor shortage. Balancing the drive for technological efficiency with the imperative for sustainability and workforce development will be the critical hurdle for concrete contractors.
Q. What has caught your interest lately in concrete?
What has captured my interest lately in concrete is seeing contractors creatively leverage existing (Trimble) technology, particularly robotic total stations, beyond their typical uses.
I recently heard a story from a contractor who, faced with a particularly complex residential foundation with numerous angles and varying depths, used their robotic total station not just for initial layout, but to continuously check formwork alignment and pour heights in real-time as the concrete was being placed. This proactive, almost "live" quality control directly impacted their field productivity by catching minor discrepancies immediately, preventing costly reworks that would have required breaking out cured concrete. It was a fantastic example of a contractor pushing the boundaries of existing tools to innovate their on-site process.