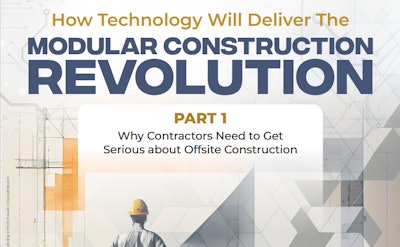
This article is part one of the FULL Report: How Technology Will Deliver the Modular Construction Revolution, a three-part series that highlights why contractors need to adopt offsite construction technology and what technology is currently available.
Use the navigation bar below to maneuver through valuable industry insight:
- CURRENT ARTICLE - PART 1: Why Contractors Need to Get Serious about Offsite Construction
- DOWNLOAD THE PDF *Save to your desktop for easy reading & reference
- PART 2: The Rise of Software for Offsite Construction
- PART 3: Offsight Builds Out ERP for Modular, Panelization and Volumetric Construction
- FULL Report: How Technology Will Deliver the Modular Construction Revolution
Modern methods of construction, offsite construction, manufacturing blended construction—regardless of what you call it, these are the technologies to help you execute against these growing project delivery systems.
Why is Construction Moving Off Site?
- Better utilization of employees
- Quality-controlled environment
- Reduction in weather-related delays
- Lower embodied carbon
- Reduces material and tool theft from job sites
What Technology do Building Teams Need to Take Advantage OF?
- Shop-based materials requirements planning (MRP)
- Configuration-based software so projects can be comprised of increasingly standardized components
- Traceability tools to satisfy inspection requirements on site for closed panels
- Logistics software to manage work on site
- BIM and preconstruction technology capable of supporting Design for Manufacturing and Assembly (DFMA)
Mechanical electrical and plumbing contractors, precast concrete companies and manufactured home builders have long practiced various forms of offsite construction. But several trends are converging that will result in more value being placed upon shop-based environments.
Constrained labor availability means the labor efficiencies of assembly line or workstation-based environments will help building teams maximize labor productivity. Pressures by owners to lower cost and improve schedule and quality outcomes also favor the controlled shop environment. Shop-based fabrication also reduces the embodied carbon represented by the construction process, making it one way for building teams to satisfy project owners’ sustainability mandates.
According to a study by Dodge Data & Analytics, 50% of contractors find that using offsite construction methods like prefabrication and modular construction improves the cost of their projects compared to projects that do not use this approach. In addition, 42% find it improves schedule, 34% quality, and perhaps most crucially these days, 30% supply chain management.
“Panelized systems or multi-trade components focus on transferring on-site construction activities into a factory setting to help produce higher quality, more consistent products and reduce on-site labor,” International Code Council Vice President for Innovation Ryan Colker wrote on ForConstructionPros.com. “This is often a low-risk approach that also reduces on-site waste while offering decarbonization benefits. With nearly 30 percent of all building materials delivered to a construction site ending up as waste and the possibility of off-site constructed projects providing embodied carbon savings of up to 45 percent, this can create substantial sustainability benefits to communities worldwide.”
Proven Method Growing in Importance
Between 1969 and 1974, Housing and Urban Development Secretary George Ronmey oversaw Operation Breakthrough, a demonstration of the value of industrialized, factory-built construction methods in an attempt to catch up with successful programs in the Soviet Union. Operation Breakthrough saw the development of 22 housing systems including volumetric modular and panelized production. About 40 manufacturers participated, erecting 3,000 units at nine sites across the United States.
McKinsey has predicted that the size of the modular construction market could reach $130 billion in the United States by 2030. According to data from the National Insulation Association (NIA), offsite had crested $85 billion in 2020 globally.
These facts are some of the drivers behind contractors making the investments necessary to create more value in a shop-based environment rather than on site. According to a 2023 data set from Autodesk, 54% of AEC companies plan to invest more in sustainability in the coming years. This pressure is coming largely from customers (82%) versus government or regulators (78%). Despite an increasing focus on environment, sustainability and governance (ESG) investing, customers also eclipsed investors (76%) as a source of pressure for increased sustainability in construction. The Autodesk study also found 94% of respondents expect their industry or organization to make sustainability focused changes in the coming years and more than half indicate they will make these investments over the next three years.
The Autodesk study further found that 73% of companies in the AEC sector plan to invest in technology to deliver improved project outcomes and 70% plan to invest in product and/or service innovation.
All of these pressures to improve project outcomes and reduce environmental impact favor more offsite, modular or panelized construction.
The Role for Technology
Just as project delivery systems like design-build or engineer-procure-construct place certain demands on the construction software and technology a building team relies on, so does modular construction.
Technology for offsite construction is evolving to meet this demand. Existing construction software applications are evolving new functionality or forging partnerships with enterprise resources planning (ERP) and other software used by panel shop partners and others.
____
Full Report: How Technology Will Deliver the Modular Construction Revolution
Navigate to your next insightful repost:
- CURRENT ARTICLE - PART 1: Why Contractors Need to Get Serious about Offsite Construction
- DOWNLOAD THE PDF *Save to your desktop for easy reading & reference
- PART 2: The Rise of Software for Offsite Construction
- PART 3: Offsight Builds Out ERP for Modular, Panelization and Volumetric Construction
- FULL Report: How Technology Will Deliver the Modular Construction Revolution
____