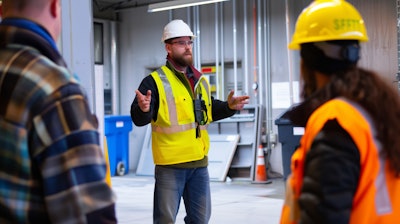
"Creating both in person and digital online instruction has been incredibly beneficial to meet the needs of different types of learners."
-Matt Dole, director of workforce development from Lighthouse Electric
IRONPROS: What business problems were you trying to address with technology and what technology did you decide to adopt?
Matt: Essentially, we were looking for a way to eliminate unforeseen challenges as early as possible by generating standardized, scalable, and flexible processes, deliverables and digital outputs that would fit at least 80% of our industry’s needs. We were looking to be proactive in our approach as opposed to reactive to the common problems that arise in electrical construction.
IRONPROS: What was training employees to use the new technology like? What challenges did you encounter during training?
Matt: First, we had to develop standardized processes based around what we felt were our best practices. Then we developed standardized trainings to reduce employee learning curves and reduce variation between different projects and project teams.
IRONPROS: How did you manage varying employee learning and training curves?
Matt: Standardization has been the key here. All our trainings can be broken into scope-based work. We can focus on the skills you need for your current activities and then provide continuous training in the future as your projects and scopes of work evolve over time.
IRONPROS: What were the most effective training tools or strategies you implemented to meet your goals?
Matt: Digitizing our information workflows was huge! Creating both in person and digital online instruction has been incredibly beneficial to meet the needs of different types of learners.
IRONPROS: In addition to training, what are the hidden challenges in adopting new technology for construction businesses?
Matt:Information and technology overload. It is easy to forget where people are currently in their adoption of technology when you work with it day in and day out. It’s important to keep things simple and not push for too much technology adoption too quickly. Technology changes so quickly these days that a new digital tool might emerge before you get feedback from the previous tool. This can hinder continuous improvement since you aren’t able to refine your processes before you try something new. This can also lead to information overload for the end user who never gains a level of comfort before things change.
IRONPROS: Please provide an overview of Lighthouse Electric and its mission.
Matt: Lighthouse Electric was formed in March of 1984 as an electrical construction firm, concentrating on commercial, institutional, and industrial projects and are now one of the region’s largest and most well-respected electrical contractors and have completed some of the most technically challenging projects in the Eastern United States. They believe collective capability is at the core of what sets Lighthouse Electric apart.
Below are some ways that this collective capability comes to life:
i. Safety
- Safety is in the lifecycle of everything we do, from estimating and scheduling to installing in the field.
ii. Scheduling
- Just like Safety, this runs the lifecycle of everything we do.
iii. EVM (Earned Value Management)
- This is one of our newest Core Processes and is putting us in a new category for financial responsibility. We can now have a firmer understanding of the health of projects earlier, which is a win for us and our clients.
iv. Estimating
- From conceptual to hard bids, we have the ability through our Estimating teams to tackle any request that comes our way.
v. Engineering
- This is a new service Lighthouse Electric is offering. We can now perform Design/Build and Design/Assist projects in-house. We will always have a need for our valued engineering partners, but from an early pre-contract perspective, this gives us a new advantage we have been searching for.
vi. Planning
PLD (Planning/Layout/Design)
- This is the 2D version of the design world. The PLD team is primarily composed of IBEW journeymen electricians with a high understanding of electrical code and installation procedures. The PLD Team lays out the project in Bluebeam before handing off to the VDC team.
VDC (Virtual Design Construction)
- This is the 3D version of the design world. The VDC team takes what the PLD team has laid out and inputs it in REVIT.
vii. Supply Chain
- This is an integral part of the operations process. Procurement of electrical goods has become a hot topic since COVID-19. The Supply Chain team is often the unsung hero of the project.
viii. Fabrication
- Prefabrication has become a cornerstone of what we do, removing fabrication from the jobsite to a controlled and safer environment which results in a more consistent high quality output.
ix. Field
- Everything we do is to make the field operations more efficient with time and resources. Labor continues to be the largest risk in our industry. Utilizing the above-mentioned steps, we believe we can attract the best talent and allow them to spend time where it is most needed.