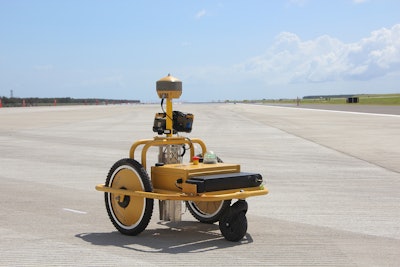
Forward-thinking highway contractors and surveyors in North America already rely on robots from TinyMobileRobots for surveying, staking and roadway pre-marking. A minority investment deal announced February 4 from German industrial group Stihl through its venture arm Stihl Digital will help the Malling, Denmark-based robotics company raise its profile in the Americas and extend distribution into South and Central America and Eastern Europe.
A leg up in the Market
In a phone interview the day after the announcement with ForConstructionPros, TinyMobileRobots Founder and CEO Jens Peter Kristensen described the upside of the new ownership arrangement, the technology that enables the wheeled robots to lay down position markers more quickly and accurately than people and some of the indoor use cases they will grow for the technology in the months and years ahead.
“The good thing is that Stihl and TinyMobileRobots are so different,” Kristensen said. “Stihl is a mature company with long product development lead time. They make sure none of their products fail. We are quick to adopt but take more risks. That means our customers may need more support and more after-sales help with our products than Stihl. Stihl is in red ocean markets competing on quality—we are in a blue ocean market competing more on functionality. Our customers need to be happy, but are a little more accepting that there are a few more glitches that need to be corrected. Even if we were making the same things, we are not competing because we have different approaches.”
STIHL Digital acquired 23.8 percent of the company, buying out a state-funded investment managed by venture capital firm Borean Innovation. Private investor Anders Fauerskov, former co-owner of TC Group, will continue to own part of the company. TinyMobileRobots has in the five years since its founding come to dominate the market for robotic positional marking, and while it owns half of the United States market for like products sees North America as a growth region.
The two companies can also engage in technology transfer internal to the ownership group according to Kristensen, but while TinyMobileRobots may enjoy greater component buying power thanks to shared ownership with Stihl, they will keep manufacturing internally.
“We are doing lining and infrastructure layout—they are not,” Kristensen said. “We can exchange technology without losing anything. We will still do the manufacturing ourselves, but we are using suppliers for all our components. It is very important for the assembly to stay here because that helps us very quickly adopt our products and maintain quality. We are not seeing manufacturing as something that Stihl can help us with but greater buying power—that is something we are looking into. We might have shared components with their current product set.”
Other robotics companies have launched line marking robots, mostly oriented towards sports field marketing where TinyMobileRobots also has an offering. Other robotics technology is making its way to market to handle the second phase of roadway painting--transverse markings, diagonals, bike symbols, school-zone markings, turn arrows. The Trimble-Boston Dynamics Spot Robot is also being outfitted with a total station to automate surveying and site layout chores, putting it in more direct competition with the TinySurveyor. The Spot application is in early stages, however, according to sources with the two companies, and it is not known whether the robot would also handle line or stake marking duties.
“In North America we have a very strong organization,” Kristensen said. “We are not going to change anything with our distribution in North America. There are opportunities for us where Stihl can help with distribution in South or Middle America and in Eastern Europe. Even though TinyMobileRobots has a leadership position, Stihl has a stronger brand, and we will benefit from the trustworthiness of that Stihl brand.”
The TinySurveyor and TinyPreMarker robots integrate with Global navigation satellite system (GNSS) receivers from major manufacturers including Topcon, Trimble and Leica. The TinySurveyor, which unlike the TinyPremarker is not sold with its own GNSS receiver, and integrates with external total stations for positioning data including height measurements. A prism mounted beneath the TinySurveyor’s GNSS antennae enables accuracy tolerances of less than one inch. The robots mark points with a standard aerosol can, making fast work of road center lines or layout of sites like solar parks. Using two points for a line or three points for an arc, the robots have application pre-marking lines on roadways and survey site staking.
A tablet app can be used to control TinyMobileRobots infrastructure robots manually, on roadway premarking projects outside of cell signal range, for instance. The robots primarily navigate using GNSS satellite signals.TinyMobileRobots
Simple and Elegant Tech Stack
The robots are only one component in an overall solution that also includes a tablet and cloud application that controls and can lock the robot. The robots do their own edge computing work to automate their precise positioning capabilities—critical in applications where they may not be able to access a cellular network. This heavy lifting is handled by the Robot Operating System (ROS) framework, which gives software access to hardware resources, provides the drivers required to run hardware and enables multiple processes to coordinate across the different pieces of hardware and components that comprise a robot. GNSS location and layouts downloaded from the cloud or installed through a USB port give the robots the information they need to navigate. TinyMobileRobots also makes a product for sports field marking that does require a cellular connection to function, but trained surveyors have a deeper skill set and the company operates under the assumption they are able to operate a GNSS-driven device more easily than an untrained consumer. The cloud application also enables TinyMobileRobots to troubleshoot robots for their customers. The tablet controller can be used to manually operate the robots through a Bluetooth connection.
A human worker needs to take TinySurveyor or TinyPreMarker to a location where it can start its work and then turn it on. The ROS and GNSS positioning data will enable the robot to do the rest. Because the robots are moving, they can use online correction services to get fixed references from around the world, taking advantage of the robot’s movement to triangulate its position even more accurately.
Using machine vision, the robots can sense objects in front of them and wait until the way is cleared before proceeding. According to Kristensen, if a turtle is crossing the right-of-way and blocks the path of the TinyMobileRobot, the robot will wait until the path is clear and then proceed on with its job.
“It has sensors that detect obstructions and can navigate around them,” Kristensen said. “We have chosen to use ultrasonic which is unusual. Lidar is more frequently used, but it is also more sensitive to dirt and water.”
The application of the technology is narrow enough that ROS and machine vision, paired with GNSS are sufficient to enable the robots to do their jobs without more sophisticated intelligence that would require the more the robust artificial intelligence provided by a neural network.
“I love neural networks, but we keep it simple,” Kristensen said. “We have not seen the need for a neural network. The robot has to make a line—if there is an obstruction, it has to stop. It cannot go around. Indoors at a construction site there would be many obstructions.”
Infrastructure to Indoors
Yet indoors are exactly where the robots will go next, although probably at a phase in construction when a concrete slab is clear of debris.
The company has developed a PropTech-robot for measuring large indoor areas such as high-rise construction sites, storage buildings, warehouses and production facilities, where millions of square feet otherwise have to be measured manually. By using TinyMobileRobots, these time-consuming tasks can be optimized significantly.
“The main challenge indoors is that the construction industry is used to having a lot of mess on the work places—pallets, garbage, and then they also have construction related parts. Indoor, the workflow has to be changed to accommodate the robots. But if you want accurate and fast layouting, the robot is extremely efficient—five to 10 times more efficient than a man doing the work.”
On construction sites with many obstructions on the ground, the Spot Robot may be appealing, according to Kristensen, but TinyMobileRobots will have strong use cases when extremely accurate line marking capabilities are critical.
“I used to see Spot as a competitor but now I see that we are offering very different use cases,” Kristensen said. “Outdoors we are using GNSS technology down to half an inch, indoor there is a lot of need for marking for construction and there, we are down to 1/10th of an inch. This is possible with laser control systems like a total station. We can also use a total station outdoors. But indoors, marking location for utilities, walls—those are the two main applications depending on construction methods. Sometimes you can use the robot for marking the wall, and sometimes when casting in place mark the utilities and then on top of that you mark the walls. The use case for Spot currently is scanning an area—that is not where we want to go. Their strength is going where our robot cannot move. We can achieve accuracy in marking the Boston Dynamics -Trimble Spot robot cannot. The robots have extremely accurate wheels and tools to position itself and that is our strength.”
BOTTOM LINE: More road contractors and survey crews will likely adopt robotics as the value proposition is high and return can be realized almost immediately. Indoors, wheeled robots offer an attractive marketing option albeit in limited applications.