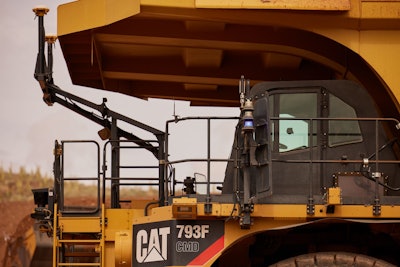
Caterpillar’s investment and innovation in autonomous haulage with Cat MineStar Command for hauling has resulted in hundreds of trucks operating at dozens of sites across three continents.
Offering multiple layers of protection to support safety, the Caterpillar autonomous haulage solution drives hauling predictability at operations.
Deploying Cat MineStar Command
Leveraging decades of development and more than 11 years of operational experience, trucks equipped with Command for hauling have now surpassed 8.6 billion tonnes (9.5 billion tons) of material autonomously hauled. MineStar Command manages the autonomous ecosystem to increase haulage through less idle time, bunching at the loader, unnecessary empty travel and wasted fuel.
“Caterpillar is an industry leader in autonomous technology, and there is a reason for that. Our deeply integrated solution provides demonstrated value to our customers in the areas of safety, productivity, and efficiency,” said Denise Johnson, group president of Caterpillar Resource Industries. “We continuously improve and push ourselves to be the very best. We know it takes a combined focus on people, process and technology to ensure long-term sustainability.”
Caterpillar continues to develop and integrate new MineStar capabilities to support battery electric technology and charging solutions. These new offerings will manage the orchestration of energy and production across a mine site.
“The mine site of the future will be more complex than ever before as customers look to achieve the same production goals, while balancing new challenges such as energy management. We believe the linkage between automation and electrification will unlock the potential for a complete ecosystem integrating technologies to meet or exceed the demands of today and tomorrow,” said Johnson.
Command for hauling supports safety by removing haul truck operators from potentially hazardous conditions. Cat autonomous trucks can detect and react to surrounding conditions and obstacles as well as interact safely with staffed equipment and light vehicles using a combination of advanced onboard perception system and proximity awareness. These technologies enable the trucks to maintain optimal following distances and safe operating speeds and, upon detecting an obstacle or anticipating an interaction, automatically stop or slow the truck’s speed.
Cat MineStar Solutions impact the hauling operation in multiple ways – enabling fleet assignment, fully autonomous haulage, equipment tracking, production recording, material management, business insights, safety solutions, maintenance solutions and more.
Caterpillar
Retrofit Kits
With retrofit kits available, today’s range of Cat mining trucks capable of fully autonomous operation span the 190- to 370- tonne (210- to 410-ton) class sizes, including the Cat 789D, 793D, 793F and 797F, as well as the electric drive 794 AC and high-altitude 798 AC models. Beyond haul trucks, the Cat 789D water truck platform can be equipped with Command for hauling, providing a fully autonomous solution to manage haul road dust. Soon, Caterpillar will expand autonomous haulage to its 139-tonne (153-ton), Cat 785. These models can be equipped with a portion of the autonomous kit from the factory, making them “Command-ready” to reduce installation time in the field.
Commodities mined around the world using Command for hauling include iron ore, copper, gold, coal, oil sands, lithium and traprock. The trucks face extremely challenging mining conditions, from the 40˚C (104˚F) heat and red dust in Western Australia to sub-freezing -40˚C/F temperatures of the Canadian oil sands. They also operate in the deep pit copper mines of South America.
“We develop software specifically for the application, so the trucks can efficiently drive through the axle-deep ruts of the oil sands or traverse the grades at deep pit mines,” said Sean McGinnis, vice president and general manager of technology and global sales support. “Our engineers remain in close contact with mining customers and continually enhance software functionality, which is critical in the world of technology to have the latest advancements in real-time.”
MineStar Solutions offers a range of remote and autonomous applications besides autonomous haulage to help further optimize mine site operations. This includes Command for drilling to automate the drilling operation, Command for dozing to enable remote dozer operation and Command for underground to enable remote operation of load-haul-dump (LHD) machines.