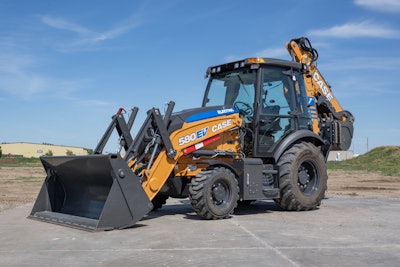
Terry Dolan, vice president, North America, CASE Construction Equipment, talks electric construction equipment trends and what’s behind the decision to go electric.
IRONPROS: Please provide an overview of CASE CE and its mission.
Terry Dolan: Our mission at CASE Construction Equipment is to make sure we’re working harder than anyone to help crews crush it on the jobsite and in their business. We do it by listening to customers, innovating to meet their needs and pushing the industry forward with swift, smooth, smart machines that improve efficiency and productivity.
That’s what we call “practical innovation” at CASE — solving real-world problems for customers with ingenuity and grit. But it’s not just a buzzword, it’s how we’ve operated for more than 180 years, and it’s how we’re leading the industry into the future. From introducing the very first integrated backhoe loader in 1957 to our largest product launch ever last year with 32 new machines, which included our first EV products. Now, we’re ramping up with the next generation of electric equipment, which includes bringing the industry’s first electric backhoe to commercial production.
IRONPROS: In its wide arsenal of heavy construction equipment, why did CASE CE choose to start with electrifying a backhoe loader?
Dolan: The 580EV was born out of a real-world customer need. In 2019, two U.S. utility companies approached CASE about powering machines from the electricity they generate. We listened and got right to work developing the first electric backhoe concept, called Project Zeus, which debuted at CONEXPO 2020.
After that unveiling, we received a tremendous amount of customer feedback that helped to keep us moving forward. Based on that feedback, we updated the look and upped the performance class from the 580N EP model that we used for Zeus to match our more popular and more powerful 580SN model. In our view, the 580EV marks a major milestone for electrified equipment, not just because it’s the industry’s first electric backhoe loader, but also because we’ve successfully electrified our most popular model.
So why the backhoe loader? It’s a versatile workhorse on the job that many crews rely on. We wanted to bring the benefits of electrification, like zero emissions and minimal noise, to a machine that teams will really want to use.
IRONPROS: What types of construction projects, working environments and applications does the 580EV electric backhoe loader excel in?
Dolan: For CASE, EVs are all about unlocking more opportunities for our customers, giving them new tools in their toolbox to meet unique challenges. The fact is, EVs can help unlock more opportunities than most people realize. Think about it: a powerful electric machine that produces zero emissions, creates minimal noise and requires no diesel fuel — it changes the game for where, when and how crews get work done.
More and more, we’re seeing projects with unique jobsite requirements. Whether it’s urban centers with rules for noise or emissions, confined or congested jobsites, nighttime projects or work that requires indoor operation — an EV backhoe loader can provide a clear advantage for these kinds of jobs.
An EV backhoe loader can also open doors to winning contracts on projects that prioritize green credentials, which are becoming increasingly common. Cities, states and the federal government are also introducing more rules and incentives to encourage sustainable construction and minimize environmental impact.
We understand that there are some jobs better suited for diesel and that an EV backhoe loader may not be right for every company. But we see EVs as a complement to our internal combustion engines, offering a way for companies to diversify their fleets and broaden their capabilities for meeting unique jobsite requirements.
IRONPROS: From a performance perspective, how does the 580EV compare with a diesel equivalent backhoe loader?
Dolan: We encourage operators to get in the cab and see for themselves how the 580EV performs. It can deliver comparable power, performance and feel as the popular 97-horsepower CASE 580SN and offers the same dimensional specifications.
Electrification also comes with some performance bonuses. The big difference operators will feel is that the 580EV provides instantaneous torque response and peak torque at any RPM. That means that with the 580EV, there is no waiting for an internal combustion engine to ramp up to meet the necessary load demands. They’ll also notice that operation is much quieter, which helps improve communication with crews on the ground and with the overall operating experience.
IRONPROS: Why did CASE CE decide to go with a J1772 L2 charger for the 580EV?
Dolan: We know charging and infrastructure concerns in the automotive space have been one of the hurdles to adoption. However, in recent years we’ve seen the automotive industry make significant investments and improvements to charging infrastructure. The 580EV takes advantage of that infrastructure by using the same automotive standard, a level 2 SAE J1772 connector, which is used by the majority of U.S. automakers today.
This allows the 580EV to charge at the same charging stations as, for example, an F150 Lightning. It also allows contractors and fleet operators to take advantage of a wide variety of charging solutions and supplies available in the automotive world, beyond the offering directly from CASE.
IRONPROS: What should customers know about battery maintenance and care to ensure long-term battery and overall performance?
Dolan: EV models, like the 580EV, offer many advantages when it comes to maintenance. Specifically for the battery and the electrical system, there is no regularly scheduled maintenance needed. We recommend that users fully charge the machine at least once every 30 days to allow the battery management system (BMS) to balance the individual cells within the battery pack. Since the 580EV uses the battery technology from automobiles, many of the best practices for overall battery health on an EV car apply to the backhoe. These include avoiding very low states of charge and opportunity charging when it fits the jobsite and application.
IRONPROS: What types of power equipment support, or extend, the application of the 580EV on the jobsite? (portable generators, battery storage systems, charging adapters, transformers, portable PDUs, etc.)
Dolan: CASE is constantly innovating and working on new technology, and this is certainly true in the EV space. As part of our parent company CNH Industrial, we can collaborate with our partnering brands in agriculture on common challenges, like remote charging for EVs. We have no new announcements to share at this time, but I can say that charging and energy management are two key areas we are working on.
Beyond collaboration at CNH, it’s important to mention one of the key reasons for using the automotive SAE J1772 charging connector is that the 580EV can take advantage of the numerous companies innovating in charging solutions for cars. There are companies delivering charging as a service with mobile stations, companies creating dedicated off-highway battery generators, hydrogen fuel cell power stations, self-contained solar stations and many more. The J1772 connector also allows the 580EV to charge at over 130,000 Level 2 commercial charging stations in the U.S., if one happens to be located near the jobsite.