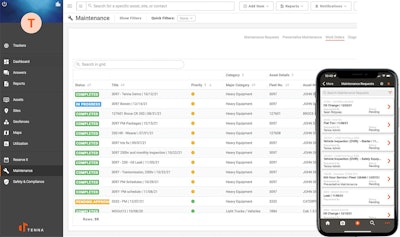
It is critical that your equipment maintenance solution ensures your fleet remains in good working condition for safe and optimal performance. Non-working assets are extremely disruptive to productivity and budget.
Tennas construction fleet maintenance software makes it easier for you and your shop staff to manage preventive maintenance and prolong your assets lifespans. Field personnel can schedule equipment maintenance or repairs directly with mechanics when required, report damage from the field using the Tenna App, submit construction work orders, log entries and capture repair documentation to help resell an asset in the future.
We help ensure your assets are kept in top shape to extend their lifespan, reduce your owning and operating costs, and improve your overall equipment management.
Maintenance Requests
- With Tennas construction equipment maintenance tracking app you can submit maintenance requests directly from the field with voice memos, text notes and on-the-go submission capabilities for ease and efficiency. Check the status on maintenance work orders to stay informed. See reports for completed maintenance. Log maintenance entries and maintain records of service at the asset level.
Preventative Maintenance
- With Tennas preventive maintenance program for equipment you can set customized maintenance recurrences based on time or usage and automated triggers when service is coming due for effective equipment maintenance management.
- Automate preventive maintenance services and update service status and progress in the shop.
- Trigger notifications to mechanics and equipment division personnel when repairs are coming due.
Work Orders
- Create construction equipment maintenance work orders to capture maintenance needs for each asset. Assign work orders to mechanics to optimize schedules and service routines. Monitor progress and status.
- Leverage work order management to monitor services for individual assets and schedule them with mechanics.
- Document parts and labor associated with each maintenance event for efficient billing and cost control.
- Capture repair needs with photos and detail.
Fault Codes
- Issues discovered on equipment and transmitted by the equipment gps tracking device help the shop understand the faults from the machine.
Diagnostic Trouble Codes (DTC)
- Issues provided by the vehicles electronic control unit (ECU) via the fleet gps tracking device help the shop understand the trouble codes and root cause of the issue.
Scheduling
- Optimize and coordinate schedules to perform maintenance around project reservations to reduce impact to operations while ensuring machines are adequately serviced in a timely manner.
Repair Documentation & Reporting
- Capture upcoming service needs at the asset level for visibility and awareness.
- Document and report on repairs and services performed for efficient record keeping and added value and during resale.
- Analyze all assets with upcoming maintenance or repair needs and see construction work order progress and status.