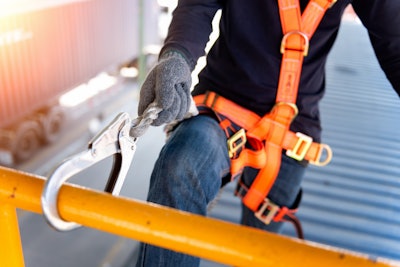
According to the Bureau of Labor Statistics, there are around 150,000 construction site incidents every year. Most of them end up as minor spine or back injuries, but there is a 1 in 200 chance of a fatal injury. And while that may not seem like much, it’s far more than in other industries. In fact, the construction industry is responsible for 1 in 5 deaths among US workers.
Naturally, many of the accidents are impossible to avoid simply because of the nature of the job. But some happen due to negligence, improper response to emergencies, or inadequate on-site safety standards. In other words, they are avoidable, but only if the management and the workers are willing to put in more effort.
Ultimately, how they decide to do that is up to the management. But here are eight methods for improving construction site safety that every firm should consider implementing.
1. Induction and Training
Before construction workers begin working, they need to receive proper safety training and induction. Training involves familiarizing with or refreshing the knowledge of standard safety procedures on a construction site. Typically, it should cover minor matters, such as the proper use of ladders, as well as more significant ones, like first aid and fall protection.
It’s important to note that training shouldn’t happen just once and never again. Construction workers should be obliged to attend sessions at least once a year. By doing so, they’ll never forget what they’ve learned, and they’ll stay informed of any new policies and standards.
But even after receiving training, workers still need to be induced whenever they start a project on a new site. After all, every site is different, with its own rules, hazards, and policies, and even the most experienced workers can’t know it all. Thus, site managers need to round everyone up and tell them what they can expect. That way, the risk of accidents and injury lowers significantly.
2. Proper Equipment
One of the leading causes of injury and death among construction workers is, without a doubt, faulty equipment. For that reason, all tools and machinery need to be checked and maintained regularly, as well as replaced when required. That’s particularly true of ladders and scaffolding. If they are defective, the construction workers using them are at serious risk of falling.
But proper equipment doesn’t entail just the kind that directly contributes to the project. PPE plays a critical role in keeping workers safe and protected from various hazards. That way, they’ll be less likely to drop a tool on another person’s head by accident or otherwise put each other in harm’s way.
On top of that, construction site managers should ensure plenty of water and shade on the site. Working outside, especially in the summer, can lead to overheating and dehydration. To avoid that, each worker should have some time to rest and refresh themselves before continuing to work. Well-rested workers are typically more aware of their surroundings and thus less likely to cause accidents.
3. Clear Communication
Communication is key at most workplaces, but it can literally save lives at construction sites. That’s why it’s crucial that it runs smoothly and effectively and that everyone fully understands every message.
Effective communication entails several things. First of all, a construction site manager should talk to the workers directly about that day’s goals. These discussions should also include pointing out potential hazards the workers might face, as well as finding ways to address them. If the construction workers know in advance what’s coming, they can prepare better.
However, it’s also crucial to enable effective communication on-site as the work is taking place. That might be a bit more challenging — after all, construction sites tend to be quite noisy. Still, workers need to hear each other, as they might otherwise miss important warnings and instructions.
Luckily, there is a solution for that too. 2 way communication headsets are an excellent investment that will improve a construction site’s safety. They typically have a headset and a microphone that allow two-way communication between workers. That way, they don’t have to walk over to each other to talk, risking injury. And in an emergency, they’re far more likely to hear warnings and react quickly.
It’s important to remember that communication is a two-way street, though. Construction site managers shouldn’t be the only ones talking — workers should feel like they can share their thoughts as well. They are the ones exposed to hazards daily, so they might come up with innovative solutions no one else would think of.
4. Near Miss Reporting
Near misses are accidents that could have caused an injury but didn’t, thanks to luck or quick reactions. Many construction site managers and workers don’t think they are worth reporting — after all, if there is no damage, what’s there to talk about?
But according to research, near misses need to be talked about as much as actual incidents. In some way, they serve as warnings. If left unchecked, they can eventually lead to injury.
Thus, it’s important to encourage construction workers to report near misses whenever they happen. They could, for example, bring them up with the site manager. If not, they might also fill out incident forms and include near misses. Whatever the case, higher-ups should be informed about them.
The next step entails understanding what caused the near miss and how to avoid it in the future. Once they’re properly analyzed, they’ll yield valuable information about prevention strategies. When site managers implement those, the likelihood of similar near misses or accidents happening will significantly decrease.
5. Housekeeping
Construction sites can get rather messy with all the tools, equipment, and materials.
Once that mess starts blocking the routes and tripping up workers, it becomes a problem. That’s why it’s crucial to tidy up regularly and properly store away any tools not currently in use.
To ensure the construction site is tidy, many companies hire workers whose job is to only take care of housekeeping. Usually, that’s the most efficient way — the actual construction workers can then fully focus on their tasks.
However, smaller companies may not want to spend additional money on housekeeping. In such a case, it’s a good idea to make a schedule and write down who’s responsible for cleaning and at what time. That way, everyone will work on it equally, and there will be no confusion.
6. Weekly Safety Meetings
An excellent way to keep up with any safety concerns on the construction site is to organize weekly safety meetings. These meetings should allow the workers to voice their concerns, discuss near misses, and offer suggestions. Similarly, the management should use them to highlight any potential hazards in future projects and propose solutions. In other words, weekly meetings should facilitate communication.
Aside from that, the staff may use weekly meetings to review the past week. Any incidents that might have happened should be brought up, and safety achievements should be praised. Ultimately, it’s a good way for everyone involved to come together and make sure they are on the same page.
7. Capable Supervision
Though construction workers need to always adhere to safe practices they’ve learned about, they aren’t the only ones responsible for construction site safety. Proper supervision and leadership exist to enforce safety standards and ensure everyone follows them.
To do that, a supervisor needs to be aware of what’s happening on the construction site and closely monitor workers. That way, whenever someone fails to adhere to safety procedures, they can be quickly corrected.
But the most important thing supervisors should do is build a good rapport with construction workers. If they succeed, they will no longer need to monitor quite as closely. Instead, the workers will be more willing to accept their suggestions and freely approach them with questions and concerns. And that’s the ultimate sign of capable supervision.
8. Encouraging Innovation
Finally, encouraging new and innovative technology and procedures is crucial for reducing the accident rate. Whenever there are available resources, construction firms should put them towards innovation. That way, they can come up with brand new solutions to help them keep construction workers safe.
For instance, thanks to forward-thinking and innovation, some construction sites nowadays have sensors that measure temperature, noise pollution, carbon monoxide, and other toxins. If anything reaches health-threatening levels, the sensors alert the workers to take certain measures to protect themselves.
Construction site safety is an important topic every manager should carefully consider. After all, sound policies, proper equipment, innovation, and clear communication can go a long way in protecting workers from injuries. And it’s not just injuries, either — in some cases, they may even save their lives.
Ultimately, no matter how much time the management spends on construction safety, it’s never too much. It’s always better to implement too many policies than too few, as well as to carefully consider which ones are effective. At the end of the day, safe construction sites will always be more efficient than those that aren’t.